Planning for Industry 4.0
Part One in a Two-Part Series
0 分鐘閱讀
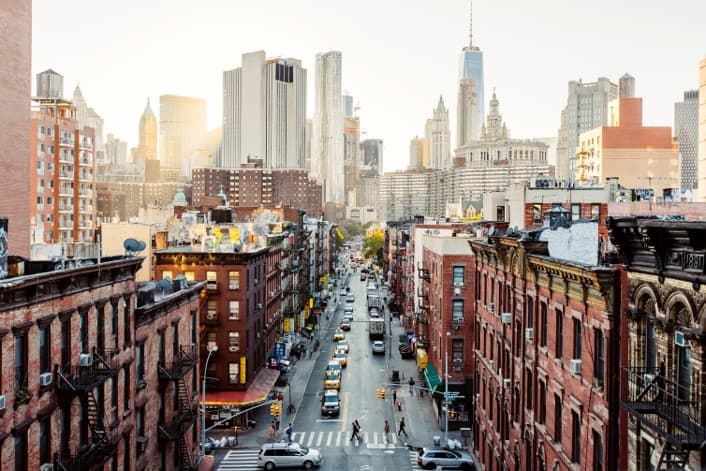
Industry 4.0 promises to deliver a revolution in how we manufacture and manage the critical infrastructural services on which we all depend. According to Gartner, it’s a burgeoning sector, something that’s worth over 60 billion US dollars this year. It’s also the subject of a lot of industry hype and knowing how to start on a 4.0 initiative can be daunting prospect. So how can critical infrastructural providers take advantage of Industry 4.0, what are the potential benefits and how best can they plan to take advantage of it?
What is Industry 4.0?
Spend even a few minutes online and you’ll probably conclude that Industry 4.0 is a term that is subject to multiple definitions. Wikipedia for example, summarizes 4.0 as the ongoing automation of traditional manufacturing and industrial practices, using modern smart technology. Ok, that’s fine but let’s refine it a little further:
"Industry 4.0 is the digital transformation of manufacturing/production and related industries and value creation processes."
It’s a topic that’s sparked intense interest as organisations look to 4.0 initiatives to help increase productivity, become more agile, accelerate innovation and ultimately decrease cost and increase profits. One of the biggest challenges any organisation will face in pursuing these goals, is how best to defend against cyberattack while still maintaining system availability and integrity.
Traditional Defences
Historically of course with strictly segregated operational technology (OT) and information technology (IT) networks, cybersecurity was both simple but also inflexible and tended to introduce latency into business processes.
Systems were not connected to the Internet. Within the business ERP and MRP systems communicated with each other. Data from the OT network at each site fed production data into the business via data diodes – unidirectional communication links that allowed data to flow in one direction only.
As a consequence, logging and archiving data was available internally but was necessarily fragmented and the inflexibility of the model created latency in business processes such as scheduling and maintenance.
An Explosion of Interfaces
Today, the same fundamental architectures and technologies are used but the advent of the industrial internet of things - interconnected sensors, instruments, and other devices – has created an explosion in interfaces between the OT and IT networks with a consequent increase in exposure to cyberattack.
With Industry 4.0, the cloud takes centre stage with ERP systems, MRP systems, equipment manufacturers and business partners benefitting from site data in the cloud that delivers a 360 view of operational network and assets in real-time. It’s a highly seductive view of the world, but there are no real blueprints on how to get there and no reference benchmarks on how to implement secure data transfer between systems of different sensitivity in a way that supports the move to 4.0.
Evolving Needs
Making the technical journey to 4.0 is really a case of evolution not revolution. The logical start point is to begin with securing the data transfer between OT and IT. This will typically involve extracting data for SIEM logging, monitoring the performance and security of the OT network. A further requirement will be to extract data from the OT network to support the predictive maintenance of OT equipment.
The next stage in this evolution is to secure the data transfer between IT to OT. Here, the requirement will typically be to secure scheduling feeds, and ensure OT systems are kept up to date with latest O/S and application patches.
Now it becomes possible to secure data transfer between the OT and the cloud, for example handling SIEM logging but this time making it possible to do cloud-based monitoring and sharing of OT data, delivering that 360 view of OT plant and assets to stakeholders wherever they are.
Enabling Technologies
This evolutionary approach requires critical infrastructure providers to acknowledge what is a very hostile cybersecurity landscape. Cyberattacks on critical infrastructure are growing in frequency and potential severity. Whether it’s Stuxnet attacking systems using a combination of zero-day attacks, Triton targeting industrial safety technology from Schneider Electric, or Shamoon 3 targeting the oil, gas, energy and telecom sectors across the Middle East and beyond. Defending against cyberattacks is a persistent challenge.
If you’re going to share data across physically, logically and administratively separated networks in a reliable, secure and interoperable manner, you need enabling technologies that ensure availability, integrity and confidentiality.
These technologies must support the ability to reliably extract data from OT plant and assets. Business leaders must do this in a way that’s scalable and that supports the transfer of data over modern bi-directional protocols, and in a way that absolutely ensures the integrity and confidentiality of the data.
In my next blog post, we’ll take a look at how Forcepoint products and solutions can underpin the move to Industry 4.0.
- Zero-Day Exploits and Vulnerability DisclosureRead Blog Post
X-Labs
Get insight, analysis & news straight to your inbox
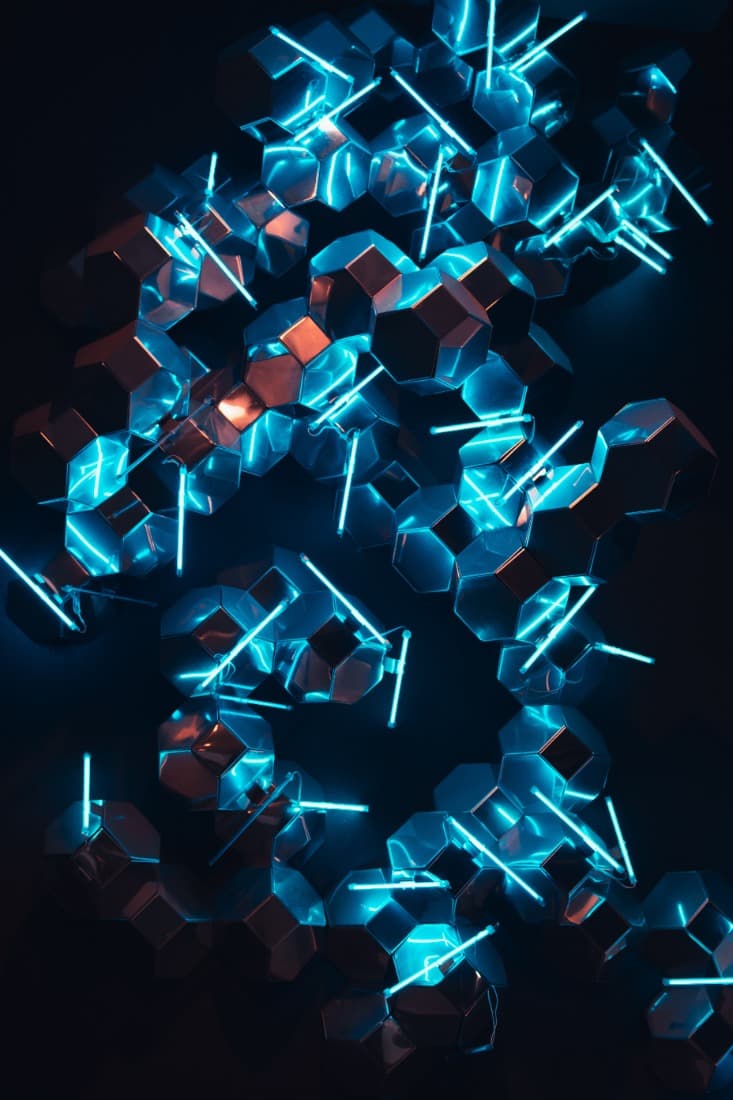